混泥土脱模剂原理
混泥土脱模剂有耐化学性,在与不同树脂的化学成分(特别是苯乙烯和胺类)接触时不被溶解。脱模剂还具有耐热及应力性能,不易分解或磨损。
那么,你知道什么是混泥土脱模剂的应力性能么?来看看吧:
聚合物在挤出、注射、压延、模压和薄膜拉伸等成型加工过程中必然受到应力的作用,当受应力作用时,聚合物的结晶过程会加速。其主要原因是聚合物受拉伸和剪切作用时,大分子沿受力方向伸直,且生成有序区,诱发成核,使得晶核形成时间缩短,晶核增加,结晶速度加快,且随拉伸速率和剪切速率的增加而增加。
内应力的实质为大分子链在熔融加工过程中形成的不平衡构象,这种不平衡构象在冷却固化时不能立即恢复到与环境条件相适应的平衡构象,这种不平衡构象的实质为一种可逆的高弹形变,而冻结的高弹形变平时以能形式贮存在塑料制品中,在适宜的条件下,这种被迫的不稳定的构象将向自由的稳定的构象转化,位能转变为动能而释放。
当大分子链间的作用力和相互缠结力承受不住这种动能时,内应力平衡即遭到破坏,注塑就会产生不良反应,影响出产产品品质,为此,采取措施降低应力影响是很重要的。
除了控制温度等生产条件外,因混凝土制品脱模剂的耐应力性能优势显著,为混泥土产品生产提供更多保障。
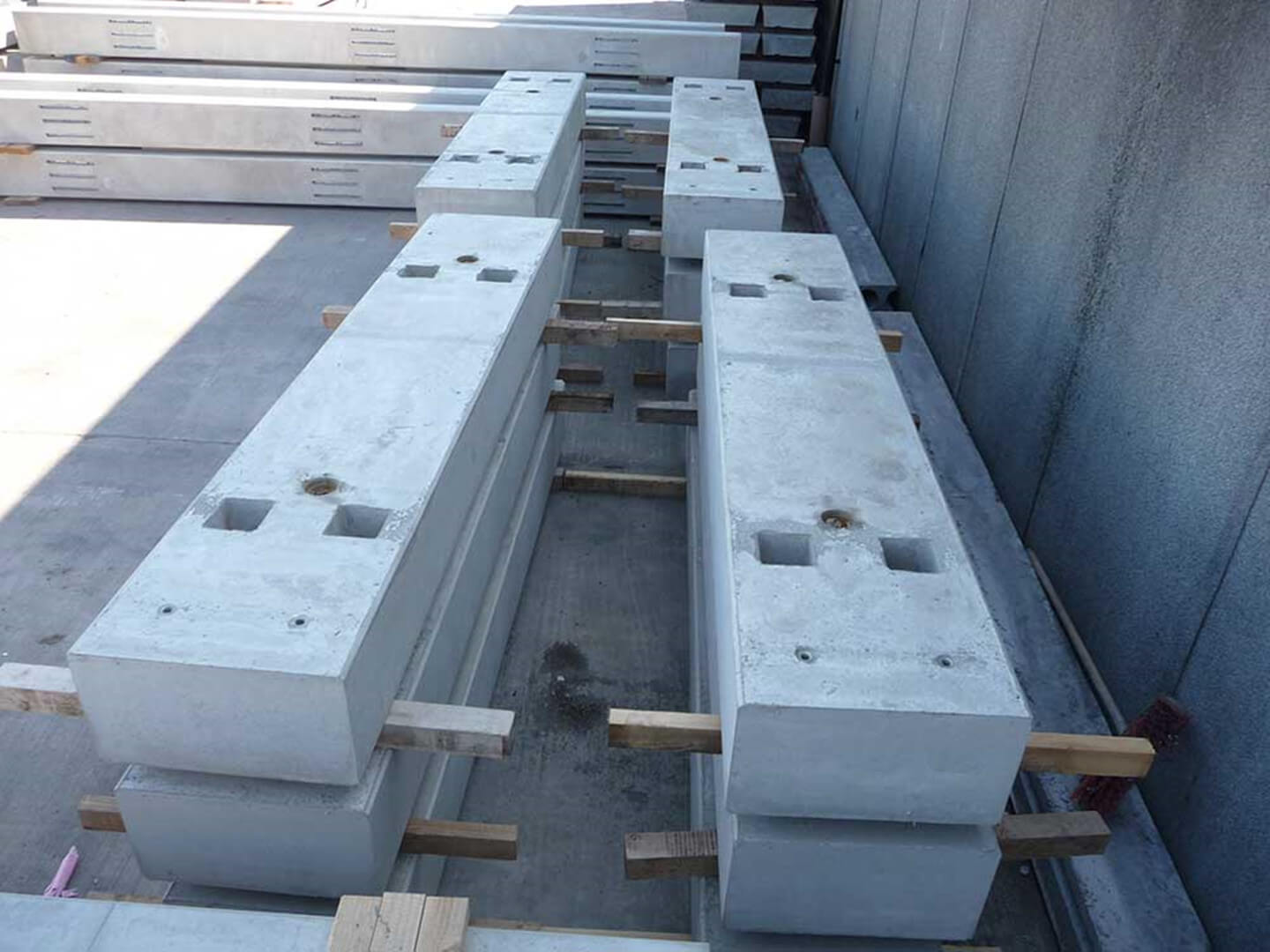
脱模剂使用方法
于大多数液体状内脱模剂都是酸性的,所以在使用中要注意以下问题:
1.在使用碱性填料时,如碳酸钙,酸性脱模剂会与之起反应,引起混合料的粘度增加,但不会影响脱模效果;
2.在使用对酸敏感的颜料时会导致颜色变化;
3.如果填料为氢氧化铝,酸性脱模剂除了会使混合料的粘度增加外,还会在混合料固化过程中放出水份,导致气泡、裂纹等问题。
通常,混凝土模板脱模剂的起始用量为树脂量的1%,有效添加范围是基于树脂重量的0.75-2%。应根据实际情况适当调整。
1.薄壁的简单型材,用量可以适当少些,比如0.8%或更少;
2.在高填料体系内,应提高内脱模剂的添加量,但内脱模剂添加量过多,会延迟固化;
3.厚壁或形状复杂的型材需要多加一些;
4.在拉挤生产中,如果阻力过大又找不到原因时,就需要适当增加脱模剂用量。在使用时应注意加料顺序,在混合时应在加入固化剂、填料和其它树脂添加剂之前,将内脱模剂加树脂体系中并混合均匀。这样可以达到最佳的脱模效果。
脱模剂配方
脱模剂有两种配方:
第一种:水基型
脱模剂基本组分:石蜡5~20份,硬脂酸5~8份,植物油5~10份,助乳化剂5~8份,氢氧化钾计算量,其他辅料适量,尼泊金乙酯适量,去离子水至100份。将石蜡、硬脂酸、助乳化剂、辅助油性原料加一容器中加热至60~80℃熔化,将水、碱剂、辅助水性原料等放在另一容器中,混合均匀加热至80~90℃。
使油相与水相温度基本保持一致,然后在剧烈搅拌下将水相慢慢加入到油相中,慢慢乳化、转相,搅拌速度随乳化温度降低而逐渐减慢,搅拌至室温后出产品,得白色水包油型乳剂。得到结果表明,脱模效果跟性能测试都很不错。
第二种:聚氨酯水性脱模剂聚氨酯水性脱模剂
由下列重量百分比的组分组成:
乳化蜡液:10%~15%;
甲基硅油乳液:15%~20%;
改性硅油乳液:5%~8%;
去离子水:50%~55%;
乳化剂:4.5%~6%;
添加剂:0.5%~1%;
防腐剂:0.3%~0.5%。
这种水性脱模剂,主要应用于聚氨酯制品生产过程浇注成型后离型,给予多数聚氨酯成型良好的脱模效果。其特点是该产品以水为分散相,形成的水溶物既具备使聚氨酯泡沫脱模的功能,又具备生物降解性,无VOC等有害物质产生,环保性强;而且水作为稀释剂,无污染易得,低成本